Agrochemical Production
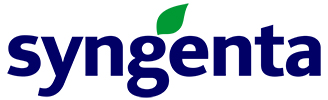
C-MAC provided:
- A complete turnkey system for optimising multi-stream product manufacturing.
- Facilities for the plant chemist to develop products and modify recipes without the need for software expertise.
- A plant simulator system for proving unit operations and recipes off-line and for training operators.
- Comprehensive historical records for quality assurance and process development.
- A broad-ranging support package, including 4 hour call-out response.
The plant
The plant consists of four main areas, namely: raw materials handling, reaction stages, a product storage stage, and a filling line. Continuous control is required, with a high level of automation and minimum operator involvement. The system provides an operator friendly man-machine interface employing modern technology which includes computer graphics for mimic displays and interaction with the plant items shown on the mimics using point and click devices.
The reaction stage consists of three parallel streams each of which includes two reactors, pressure filters and other ancillary vessels. Reactions may require up to four parallel operations to ensure minimum batch times and optimum process yields, a requirement which is easily met by the C-quin system.
Control loops are implemented in the control system, rather than by discrete controllers. Valves and motors can only be operated via computer controlled phases to ensure safe state operation. These phases are normally under recipe control, but may be initiated manually if required.
Interfaces are provided to the drum filling line, to give the operators up-to-date status information and allow a degree of remote control capability.
The C-MAC C-quin system
The C-quin process control system uses the powerful Industrial single board computer in conjunction with other industry standard for functions such as peripheral communication and I/O interfacing. Facilities provided by the system include analogue and digital I/O control (with around 1,300 I/O connections), implementation of all types of control loop (PID, cascade etc), an interface to the supervisory system for work packages, multi-thread phase execution, parallel check phases, graphics workstation support (HMI) and manually initiated operations.
The C-quin supervisory system provides full automation of recipe creation and editing, batch scheduling, control recipe records are available in ASCII text files for easy post batch analysis, either with the C-quin analysis package, or using standard spreadsheet or database programmes. A powerful feature of the C-quin architecture is the ability to support multiple control computers. In this case, five computer systems, one for each stream, one for the services (common plant items) and one for the material handling section, are all interconnected via a network to provide a robust and flexible solution.
Safety
The C-quin system also provides additional safety features to protect staff, the environment and the plant. Check phases operating in parallel with hard wired trips are provided to monitor such parameters as valve states, temperatures and fill rates. Unexpected changes during the process, indicating, for example, a runaway exothermic reactions, a failed valve or an incorrect charge, can then be detected and acted upon immediately and automatic software shutdown initiated if necessary.
C-MAC
In supplying a full turnkey system, C-MAC liaised closely with the customer’s production and formulation experts prior to implementation to ensure optimum unit operation performance and integrity under C-quin’s advanced recipe system control. C-MAC designed and installed all hardware and software for the control system, the plant wiring and the operator consoles. The company also provided a stand-alone plant simulator to enable unit operations and recipes to be developed and refined off-line, without risk to plant, staff or product. The simulator was also heavily utilised during the training of the operators and formulation chemists.