Resin Emulsion Production
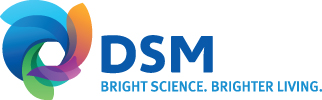
DSM Coating Resins in the Netherlands, chose the C-MAC for a number of key reasons:
- The capability of the system to provide multi-batch, multi-product manufacturing
- Its ability to handle large numbers of product recipes expressed in local language and terminology
- The ease of creating and modifying recipes for fast response to market demands
- Proven experience in replacing existing control systems
- The ease of enhancement and expansion of the system over the projected life of the plant
- The quality and speed of response of support services from C-MAC
The plant control system
The plant produces a wide range of emulsion products used in the manufacture of specialist coatings such as paints, varnishes and inks. Three independent production streams were controlled by C-MAC’s initial C-quin system, with a fourth stream being added at a later stage. In order to retain the maximum flexibility in utilisation of the available plant, the C-quin system was required to control and optimise the complex feed and transfer arrangements between the various stages. It was particularly important in maintaining batch consistency for C-quin to ensure a high degree of accuracy of the initial weighing process, and to precisely control the ingredient transfer rate into the reactors.
Simple, flexible recipe control
The nature of this business requires a large number of different formulations (recipes) to be maintained, and to be available for manufacture whenever a customer places an order. There was also a requirement to be able to introduce new product ranges quickly, with recipe creation and modification carried out by DSM Coating Resins process personnel, on site, without reference to the system supplier and without the need for specialist computer programming knowledge.
The C-quin system provides a simple recipe language, so that plant formulation experts can quickly produce recipes using plain language statements. Within recipes, facilities are built in to prompt operators to take samples at appropriate stages and to allow laboratory staff to make adjustments reflecting the sample results.
Testing of recipes is handled easily by the C-quin simulator, which provides a computer simulation of the plant and the processes involved. Even during the first months of operation of the new system, a number of new recipes had been produced, tested and used to manufacture product, in addition to the hundreds of existing recipes loaded prior to start-up.
Operator facilities
Three operator workstations are provided for day to day control and monitoring of the plant with the operational data being presented in Dutch. A fourth workstation is provided for the shift leader to monitor production and to adjust the working copies of the product recipes (control recipes) used to manufacture each batch. A fifth workstation is sited in the laboratory for fine tuning the production process based on sample analysis.
A full range of safety features is implemented by C-quin to ensure maximum operator safety; to aid adherence to local environmental standards and to minimise waste. Software checks are constantly made to detect any unexpected values of a wide variety of plant parameters, so that operators can be warned of potential problems or preventive measures can be taken automatically.
Installation and commissioning
C-MAC worked in close collaboration with the DSM Coating Resins project team from the outset. Since the project was to upgrade a live plant, careful planning was necessary to ensure minimal loss of production in changing from the old to the new system. C-MAC provided the C-quin system software and hardware, developed the application software and then installed and commissioned the system. Less than a week was taken between shutting down the old system and returning to full production under C-quin control, with operational data from C-quin being used to progressively improve product quality and yield.
Support
C-MAC provides DSM Coating Resins with a full support package to ensure that the system operated smoothly and efficiently from the outset. In addition to providing training courses both in the UK and on the customer’s site, the company also gave hot-line support which is enhanced by the provision of remote maintenance facilities via VPN link.
In the longer term, the ease of enhancement and expansion of the C-quin system will enable the customer to easily incorporate new plant into the existing control scheme.