Biocide Production
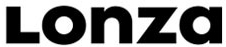
C-MAC was chosen by Lonza for their Proxel biocide production plant. Proxel is used in a wide range of domestic and industrial products, such as wallpaper, paint and adhesives. C-MAC was required to meet the following objectives:
- A proven combination of control system and design team capability.
- Support of multi-stream product manufacturing, where the plant chemist without software expertise can develop new products and modify existing recipes.
- A low cost simulation system for operator training and for recipe and unit operation testing.
- Detailed historical records for quality assurance and process development.
- Comprehensive system support, including a 4 hour response to call out.
The plant
The Proxel plant consists of more than 22 vessels (units). These being main feed, reactor, holding and mixing vessels. The product is produced over several complex reaction stages, each of which must be controlled to very tight tolerances to achieve the desired product quality and yield. These reaction stages require a parallel operations capability, to ensure minimum batch times and optimum process yields, a requirement which is easily met by the C-MAC C-quin system. The C-quin system for this application has in the order of 500 I/O connections to the plant to allow fully automated monitoring and control of all plant parameters.
The C-quin system
The C-quin system uses the powerful Industrial single board computer with other high accuracy subsystems for peripheral communication, plant I/O interfacing etc. The C-quin system provides full automation scheduling, batch manufacture, process data logging, batch record creation and archiving. Batch records are in ASCII text compatible files, for easy analysis, either with the C-quin management information system, or using standard spreadsheet or database packages.
Operator interaction with the plant is provided by three graphics workstations, which depict the plant and current processes in both mimic (graphic) and textual terms. Each workstation has the capability to display several hundred plant items. In addition a library of symbols for each plant item is provided. Over fifty different control loops are used to ensure the desired degree of tolerance in process parameters is obtained. The main algorithms employed are 3 term PID, digital on/off and cascaded loop.
Safety
In addition to the strict requirement for quality control, the C-quin system provides safety features to the environment, and the plant. Parallel check sequences are provided to monitor reaction and fill rates etc, such that any unexpected changes during the process can be detected and acted upon immediately. In this manner protection can be be provided against runaway exothermic reactions, failed valves and leaks.
C-MAC
C-MAC supplied a full turnkey system. In specifying the system we worked closely with the customer’s production and formulation experts to ensure optimum unit operation performance and integrity. C-quin’s advanced recipe system controls the execution of these unit operations.
In addition to providing a total hardware and software solution for the entire control system, plant wiring and operator consoles, C-MAC provided a stand alone simulator, to enable off-line development and testing of unit operations and recipes. The simulator was delivered three months prior to the installation of the control system and was extensively utilised during the training of operators and formulation chemists.
Training and supervision was provided by C-MAC, and played a major part in ensuring the smooth transition to the new control system.